¿Cómo se fabrica un dron en la impresora 3D de VEO?
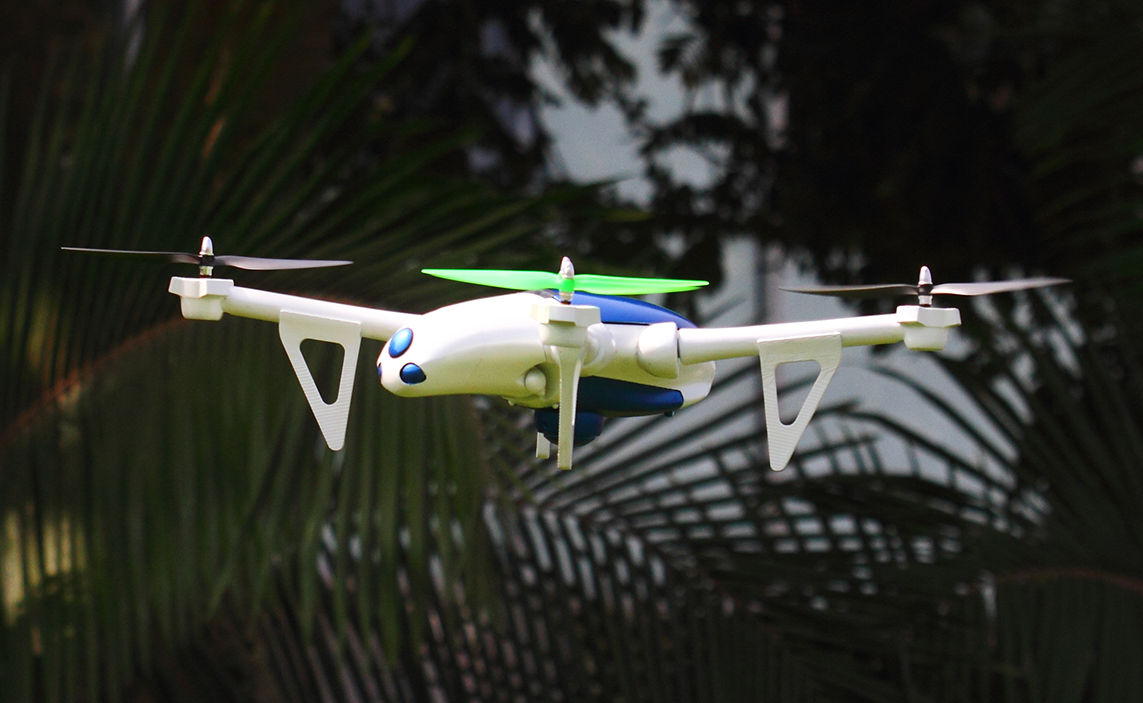
Francisco Cuellar, César Lucho, Carlos Saito y Rubén Toshiharu diseñaron un sistema aéreo no tripulado, cuyas partes se fabricaron en la impresora 3D Fortus 400mc. Somos la primera universidad del país en contar con esta tecnología.
Desde instrumentos musicales hasta prendas de vestir fabricadas a la medida. Objetos tan pequeños como la réplica de un feto o tan grandes como edificios habitables. Prótesis humanas, electrodomésticos o joyas. De plástico, titanio, tejido sintético o carne comestible. La impresión 3D parece ser una suerte de piedra filosofal capaz de crear todo lo que nuestra imaginación desee.
La PUCP adquirió en agosto la impresora Fortus 400mc, máquina que a través de la técnica de modelado de deposición fundida (FDM: Fused Deposition Modeling), le da forma al termoplástico ABS-M30, material empleado en la fabricación de moldes, piezas de uso final, prototipos funcionales y modelos conceptuales resistentes, durables y precisos. Es la primera universidad peruana en contar con este equipo.
“Ahora tenemos la capacidad de “imprimir” nuestras ideas más caprichosas y evaluar conceptos de prototipos que serían muy costosas o tomarían mucho tiempo si fueran mecanizadas. Junto con el grupo humano con el cual contamos, definitivamente nos pondrá a la delantera en cuanto a innovación y desarrollo, en comparación con el resto de universidades”, afirmó Francisco Cuéllar, ingeniero mecatrónico y candidato a doctor en robótica por la Universidad de Osaka (Japón), quien se encargó de la creación del concepto y la idea inicial del proyecto.
El equipo profesional
Antes de su presentación en sociedad, un grupo interdisciplinario de especialistas de la PUCP decidió darle un uso aplicativo a esta herramienta y desarrolló un vehículo aéreo no tripulado, también conocido como dron o UAV, por sus siglas en inglés. A diferencia de los aviones a control remoto, que son principalmente recreativos, los drones tienen una funcionalidad y llevan una carga útil (cámaras, sensores, etc.) que les permite captar información que pueda ser luego procesada para algún fin, sea este civil o militar.
Además de Cuéllar, el equipo estuvo conformado por: Carlos Saito (ingeniero aeronáutico), César Lucho (diseñador industrial) y Rubén Toshiharu (ingeniero mecánico). Ellos tuvieron cerca de dos meses para transformar bocetos a lápiz y crayón en una aeronave capaz de surcar el cielo del campus PUCP. Para la mayoría, era la primera vez que construirían un dron o emplearían esta tecnología. Extraoficialmente, bautizaron el proyecto con el nombre de “Ícaro”.
“La nave tenía dos objetivos principales: El primero era demostrar lo que se puede fabricar con la impresora 3D y el segundo, desarrollar un robot que siga la temática de la interacción robot-humano y que nos permita ver cómo se desenvuelven con las personas a nivel grupal o individual”, recuerda César Lucho.
La concepción
Debido a que el sistema mecánico de un helicóptero a escala resulta complejo y costoso, se optó por desarrollar un cuadricóptero que funcione con cuatro motores eléctricos sin escobillas. Lucho estuvo encargado del diseño conceptual y formal tridimensional de todos los componentes del dron (brazos, cuerpo, cabeza y cuello).
Como se trataba de un UAV, Lucho tuvo que aplicar principios aerodinámicos en el diseño de la nave. Para ello, contó con la colaboración de Carlos Saito, ingeniero aeronáutico de la Academia de la Fuerza Aérea de los EE.UU. Saito estuvo a cargo de las pruebas de resistencia y estabilidad (en túneles de viento virtuales) así como del análisis estructural del dron. “La forma de vuelo de este vehículo no es convencional. Debía determinar qué tan rápido debía girar cada uno de sus motores para que se mantenga estable y verificar que sus brazos no se rompan por la fuerza de las hélices al momento de volar”.
La fabricación
Posteriormente, se dio inicio a la fabricación del dron. “La resistencia y la flexibilidad del material permitió que se le diera acabados en masilla, y perforar, lijar y pintar. Todas las piezas encajaron perfectamente” recuerda Jennifer Wong, supervisora del Área de Impresión 3D de VEO. Por su parte, Lucho agrega: “La ventaja de la impresión 3D es que podemos imprimir cuantas veces y formas necesitemos para hacer las pruebas y llegar a un buen resultado. De hecho, un par de semanas antes de la presentación, una de las piezas se rompió. Mejoramos el diseño, lo mandamos a imprimir y al día siguiente ya se tenía lista la nave para una nueva prueba”.
Una vez finalizada la impresión, lo que faltaba era integrar el sistema electrónico a la carcasa, vale decir, los motores y la tarjeta de control del dron. El Ing. Rubén Toshiharu adaptó y reconfiguró el sistema de otro UAV a la nave en construcción. “Como necesitaban un piloto y ya tenía práctica con otros drones, me ofrecí para volar la nave el día de la presentación. El día previo nos quedamos hasta la 1:30 a.m. corrigiendo errores en la configuración. Hemos corrido contra el tiempo”.
La presentación
Y llegó el día. El 22 de agosto se realizó una jornada de presentación de la impresora 3D, en la que se realizaron mesas redondas con invitados internacionales, expertos locales y profesores PUCP en la que se debatió el impacto de esta tecnología desde distintos sectores de nuestra sociedad. Y durante un intermedio a media tarde, el dron recorrió el Jardín Central del campus a diversas alturas y velocidades.
“Lo bonito de esto es que estamos haciendo un trabajo interdisciplinario, no solamente entre ingenieros sino también con especialistas de Arte. Próximamente, queremos integrar a la gente de Humanidades para entender cómo funciona el grupo social en su interacción con los robots”, acota Lucho. No nos cabe duda que este solo es el punto de partida.
Mira también la edición de Siéntete Geek sobre los UAV.
Deja un comentario